The LEE Company
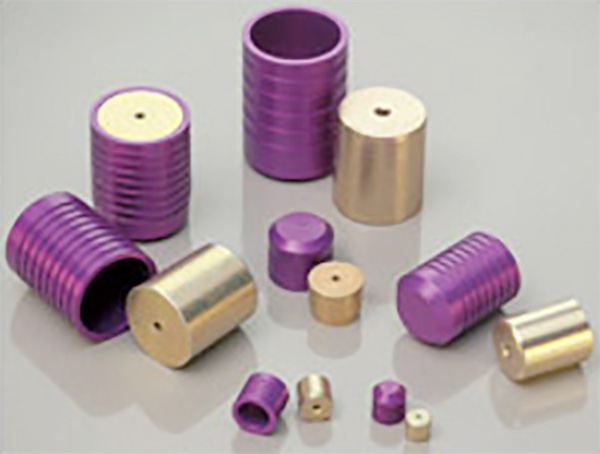
LEE Plugs
The LEE Plugs is simply the most successful method to seal drilled holes for critical applications. Over 150 million are in use on aircraft, missiles, spacecraft, machine tools, down hole oil tools, Molds – anything that requires a peremanent leak-proof seal.
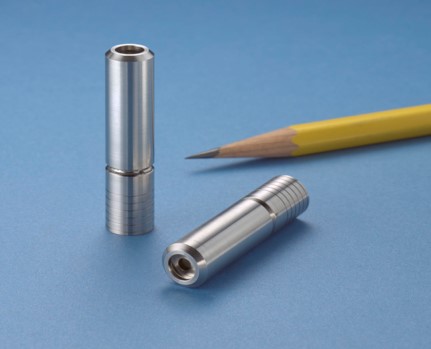
LEE Restrictors
Lee Restrictors have become the accepted “standards” worldwide. Lee Company restrictors due to their small size, light weight and proven reliability are indispensable when the flow of fluids has to be controlled. Our miniature precision flow restrictors are specified by manufacturers of aircraft hydraulic and fuel control systems, oil drilling equipment, missile controls, machine tools, and countless other products. Lee restrictors are a vital part of almost every military and commercial aircraft manufactured in the world. By employing already proven and qualified Lee restrictors in their designs, design engineers are using their own time and talents much more productively.
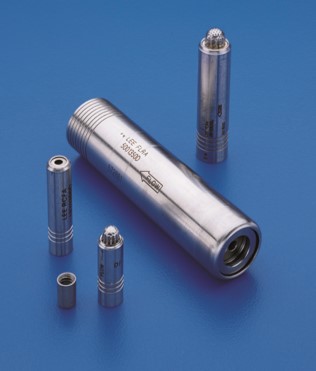
LEE Flow Control
The Lee Company makes three different types of flow metering valves; a Restrictor Chek, a Directional Flow Control and a Flosert.
Lee Restrictor Cheks combines the function of a restrictor in series with a check valve into one miniature package.
Lee Directional Flow Controls provide metered flow in one direction and free flow in the opposite direction (this function is sometimes called a one-way restrictor).
Lee Floserts are pressure compensated flow controls which provide a constant flow over a wide range of pressure drop across the insert
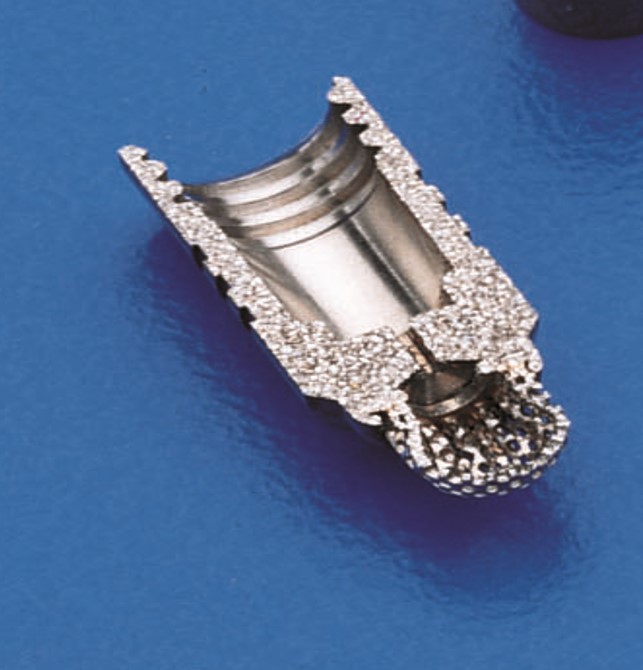
LEE Nozzles
The Lee Company offers two types of miniature precision nozzles: the Spin Jet and the Lubrication Jet. Both types are constructed entirely from stainless steel for compatibility with most industrial and aerospace liquids. Both incorporate the unique installation and retention principle used in the already proven and qualified Lee valves and restrictors. Their small size and light weight make them extremely cost effective.
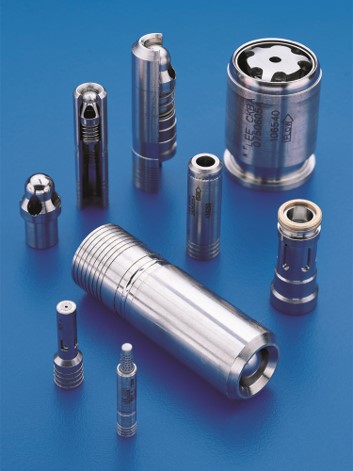
LEE Chek Valves
Lee Cheks are the smallest insert check valves available anywhere in the world. One model is only 3/32 of an inch in diameter and under 1/3 of an inch long. With millions successfully in service, some for over thirty years, Lee Cheks have proven reliability. Every Chek is 100% performance tested before delivery. Lee Cheks set the standard for size, weight, and dependability. The primary selection criteria for check valves are flow rate, packaging requirements, resistance to contamination, allowable leakage, pressure and temperature requirements and compatibility with the intended fluid and environment. Lee Cheks are available in multiple configurations that include ball-style or poppet-style sealing elements, axial or side-exit flow paths, metal or elastomeric seats, and insert or cartridge style bodies. There are also options for integral safety screens and pilot operated designs.
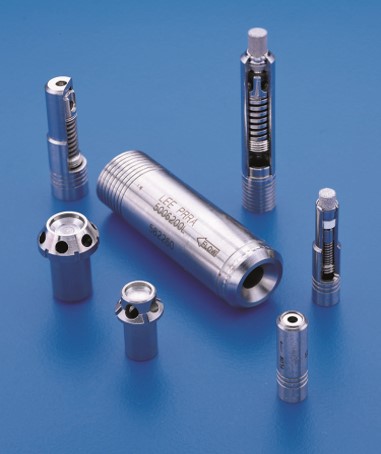
Lee Relief Valves
Lee relief valves come in a wide range of styles. Each style has been developed to satisfy specific relief needs commonly found in hydraulic systems. Safety relief valves are designed to be exercised for intermittent “pop off” applications. Pressure regulating valves are intended to operate more continuously with stable performance throughout the operating range. Thermal relief valves relieve a few droplets of fluid from a trapped volume expanding due to rising temperatures. Because these applications are very different, it is important that the correct valve is selected to ensure proper functioning of the system.
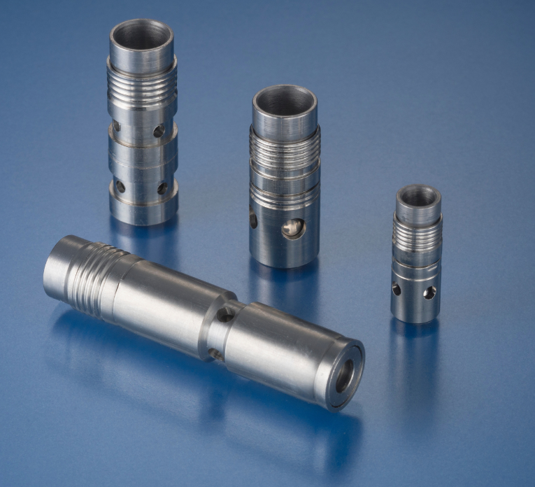
LEE Shuttle Valves
The Lee Shuttle Valve is offered in four configurations. One type is the spring biased shuttle valve with the emergency port normally closed. Another type is the detented shuttle valve where the poppet latches to close off either the emergency port or the normal port. Also there are selective shuttle valves with a non-biased, loose ball design. Finally there are inverse shuttle valves where the lower pressure inlet port is open to the common port instead of the higher pressure inlet port.
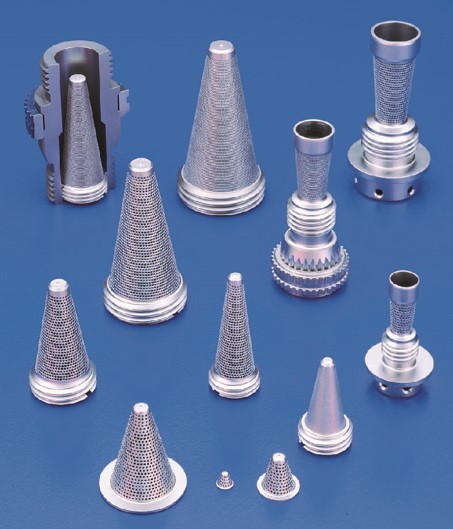
LEE Safety Screen
The need to protect orifices, relief valves, and other sensitive hydraulic components from contamination is widely recognized, but contaminant size has a lot to do with the type of protection needed. Critical components are often relatively immune to low levels of small-size contaminants, but a single large particle can cause sudden failure – possibly with catastrophic effects. While filters maintain fluid cleanliness during operation, large particles, which are built into the system or introduced later, require a different approach. Here, safety screens provide an added level of protection to the system.

LEE Piloting Solenoid Valve
Lee Miniature Piloting Solenoid Valves were designed and developed to be the most reliable, efficient, and compact solenoid valves available. The valves have been qualified to numerous aerospace performance and environmental testing standards. They have proven themselves with decades of use in demanding applications under harsh conditions ranging from the high temperatures and pressures of deep subsea oil wells to the cold and vacuum of outer space.
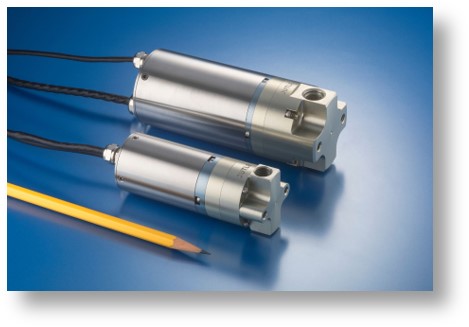
LEE Pumps
Lee Positive Displacement Pump’s unique radial piston design aids in self-priming at altitude and reduces cavitation. Lee pumps are qualified for 1000 hours of operation and to numerous aerospace specifications. As an industry leader in durability and efficiency, they are ideal for fuel systems of small to medium sized Unmanned Aerial Systems and a variety of other demanding applications.
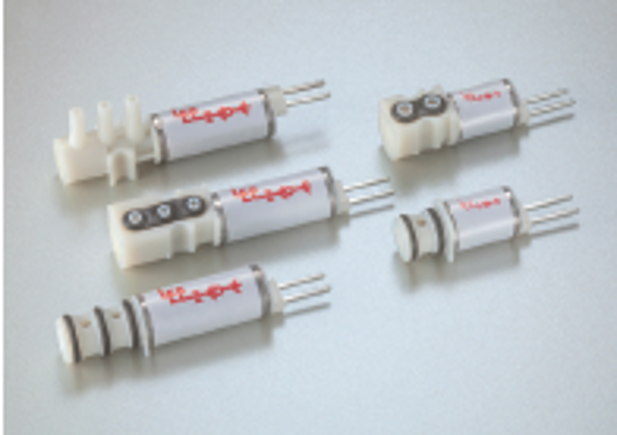
Flow Control Solenoid Valve
The Flowcontrol Solenoid Valve consists of compact, lightweight solenoid valves with low internal volume. Available in 2-Port or 3-Port designs, and in several mounting styles, these valves are easily manifold mounted, making them the perfect solution for applications where a large number of valves must be designed into the smallest space possible. These valves are generally used in oxygen delivery systems, gas analysis equipment, patient monitors, air calibration devices, ventilators, gas chromatography and dialysis machines.
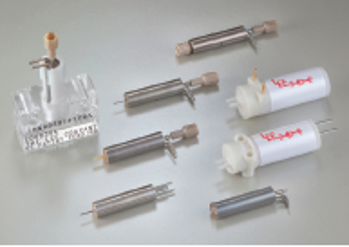
Dispensing Solenoid Valve
The Dispensing solenoid valves are designed for high speed applications requiring precise dispense volumes in the microliter to nanoliter range. These valves are generally used in medical and scientific applications, in markets such as high throughput screening, drug discovery, in vitro diagnostics, human genomics and biotechnology.
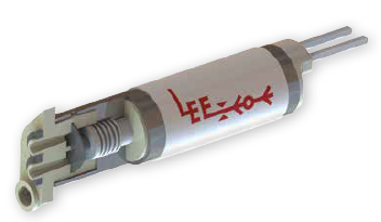
Isolation Solenoid Valve
The Isolation solenoid valves are chemically inert, isolation style valves with zero dead volume. Available in a 2-way normally closed model, the valves are rated for bidirectional flow and use a contoured internal flow path design that allows for complete flushing capability. This contoured flow path also minimizes damage to any sensitive fluids passing through the valve. The low internal volume reduces the amount of fluid required to fill the system (otherwise known as transport volume), further reducing the sample and reagent requirements.
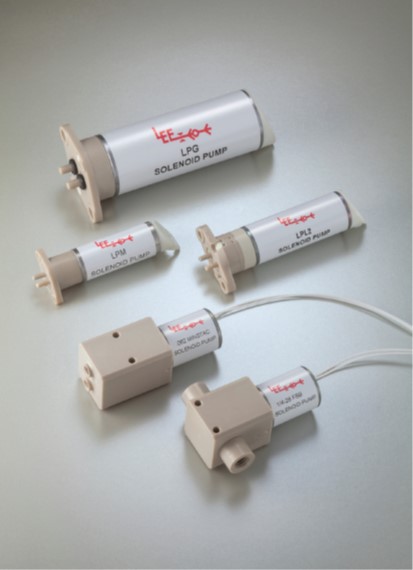
Fixed Volume Pump
The Lee Company’s Fixed Volume Dispense Pumps are solenoid driven, chemically inert, positive displacement pumps, which provide accurate and repeatable dispense volumes in a small lightweight package. Requiring a simple square wave electrical signal for operation, the pumps aspirate fluid when energized and dispense fluid when de-energized. The normally closed design with integrated check valves prevents siphoning when the pumps are de-energized.
Lee fixed volume dispense pumps are available in three different sizes to cover a wide range of dispense volumes:



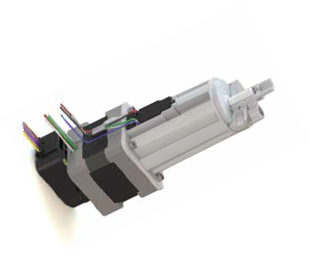
Variable Volume Pump
The Lee Company’s Variable Volume Dispense Pumps are stepper motor driven, positive displacement pumps that feature unparalleled reliability and performance. Their size, weight and maintenance free design allows for the pumps to be positioned where the fluidic requirements dictate, regardless of accessibility.
Manifold Tubing Accersories
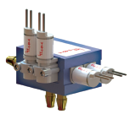
Manifold : The Lee Company Electro-Fluidic Systems Division has been an industry leader in electromechanical valve and pump technology for over three decades. Manifolds offer several advantages compared to just tubing together discrete components, such as fewer leakage points, lower internal volumes, easier assembly into the instrument, and higher reliability.
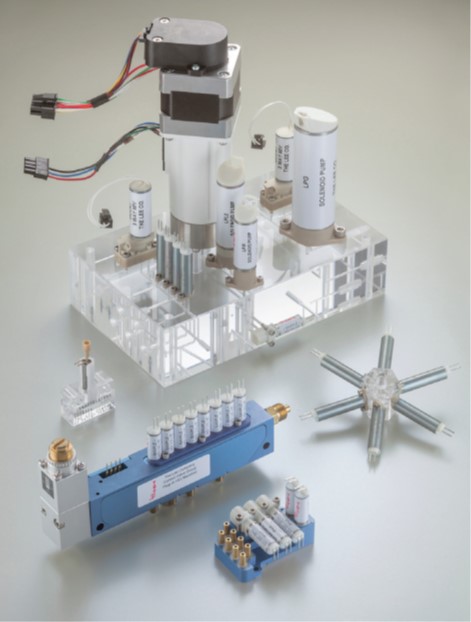
Tubing: MINSTAC, The Lee Company’s Miniature Inert System of Tubing and Components, offers the ability to precisely control flow rate, pressure, filtration and other performance factors of aggressive fluids. The basis of the Lee MINSTAC System is the unique Collet-Lock system, which allows the chamfering of PTFE tubing, and threading a specially designed Collet onto its end. This assembly provides a leak-proof connection from PTFE tubing to the wide range of MINSTAC components and fittings, all without the problems associated with the cold flow characteristics of PTFE.
IEP Solenoid Valve Series
The IEP Series solenoid valves are designed for applications requiring extended performance. Available as a 2-way normally closed design, these valves are capable of operating across a wide range of pressure and temperature without sacrificing size. These valves are typically used in applications such as scanning electron microscopes, CubeSat propulsion, precision combustion systems, oil well analyzers and cryogenic surgery devices.
The following general performance characteristics are offered in this product platform:







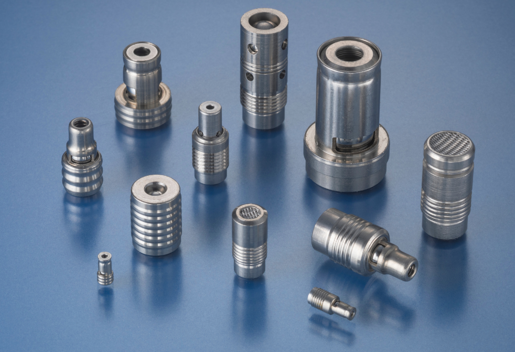
IMH Chek Valve
The IMH Chek™ is a threadless, cartridge-style insert designed for simple, low cost installation into manifolds, and is based on the same hard seat Lee Chek® designs used in flight control systems of almost every aircraft flying today. A robust design and 100% testing ensures consistent, longterm performance up to 28 MPa (4060 psid) and 149°C (300°F) or higher depending on specific application requirements.
IMH Relief Valve
IMH Relief Valves are designed to protect systems from over pressurization or to attenuate pressure spikes. These valves are not suited for upstream pressure regulation. As with the IMH Chek, the relief valve is a threadless, cartridge style insert designed for simple, low cost installation into manifolds, in the most compact package available anywhere. A high quality, metal-to-metal seat provides long life and extremely low leakage, as well as compatibility with a wide range of fluids. The Relief Valve is available in a 5.5mm size and an 8.0mm for more flow.
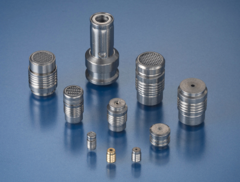
IMH Orifices
IMH Orifices are economical, reliable, highly accurate miniature restrictors. These orifices are 100% flow tested to ensure that every part is within ± 5% of its nominal flow rate. Tighter flow tolerances are available as specials. Tight flow tolerances are only possible if entrance and exit conditions are closely controlled. This provides far more accuracy than an orifice specified by hole tolerance. An ordinary hole held to a very tight hole tolerance will not result in a tight flow tolerance. IMH orifices are so consistent because they are produced in high volume by automated processes. Installation is simple using the field proven controlled expansion principle which provides retention up to 21 mPa (3,045 psid) and creates a leak tight seal
IMH Restrictor
Restrictor checks are functionally an orifice in series with a check valve, all in one package. IMH Restrictor Checks are the same size as their equivalent check valves. These valves come in forward and reverse flow directions and incorporate a screen of an appropriate filtration size for orifice diameters below 0.5mm (0.020″).
IMH Flow Control Valve
Flow Controls are functionally an orifice in parallel with a check valve — all in one package. IMH Flow Controls are the same size as the equivalent IMH check valve. Flow Controls are available in two diameters; 5.5mm and 8.0mm.
The 5.5mm version covers lohm rates from 2,000 lohms [0.5mm (0.020″)] to 10,000 lohms [0.22mm (0.009″)] equivalent orifice diameters.
The 8.0mm Flow Control covers 500 lohms [0.99mm (0.039″)] to 2,000 lohms [0.5mm (0.020″)] equivalent orifice diameters. Both sizes are available in forward and reverse configurations.
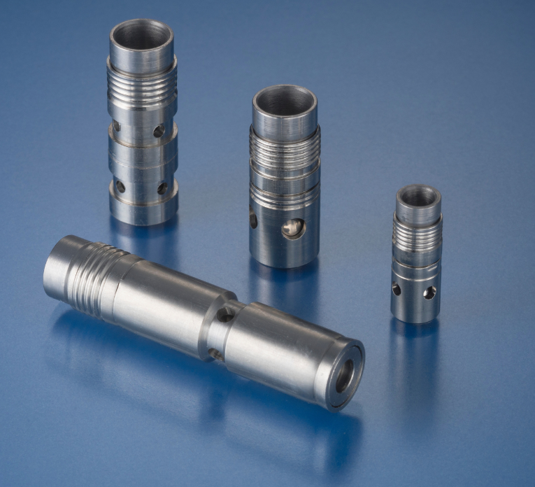
IMH Shuttle Valve
IMH Orifices are economical, reliable, highly accurate miniature restrictors. These orifices are 100% flow tested to ensure that every part is within ± 5% of its nominal flow rate. Tighter flow tolerances are available as specials. Tight flow tolerances are only possible if entrance and exit conditions are closely controlled. This provides far more accuracy than an orifice specified by hole tolerance. An ordinary hole held to a very tight hole tolerance will not result in a tight flow tolerance. IMH orifices are so consistent because they are produced in high volume by automated processes. Installation is simple using the field proven controlled expansion principle which provides retention up to 21 mPa (3,045 psid) and creates a leak tight seal
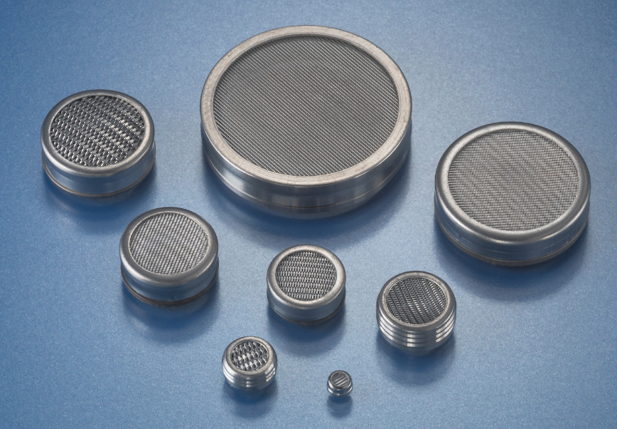
IMH Safety Screens
IMH Screens are “last chance” safety screens designed to protect critical fluid control components against rogue contamination. They are not intended to serve as system filters. The screens are constructed of stainless steel woven wire mesh, bonded together using a proprietary process that offers superior integrity and life. IMH Screens are available in Insert or Cartridge styles. Insert Screens feature an integral locking end, while Cartridge Screens are designed to be retained by the customer, or for 5.5 and 8mm sizes, retained by a separate locking end.
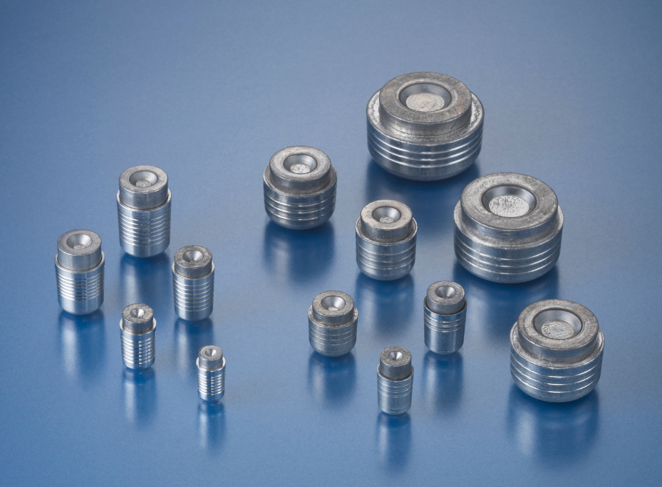
IMH Betaplugs
The Lee Betaplug is a pre-assembled, one-piece, tapered expansion plug specifically engineered to seal fluid passages in metal castings and plastic housings leak-tight, without the use of threads or sealants. Controlled expansion during installation causes the lands and grooves on the O.D. of the plug body to bite into the wall of the fluid passage, creating a leak-tight seal and assuring retention. The unique tapered design eliminates the need for tight manufacturing tolerances, and allows the designer to minimize the wall thickness required around the plug, even for brittle housing materials